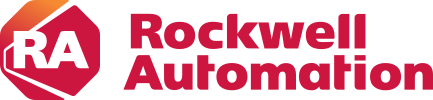
新篇章由我们书写!罗克韦尔自动化公司是全球工业自动化和数字化转型的领导者。我们将人类的想像力与科技的潜力结合,创造出更多的可能性。
- 提前识别因模具设备磨损导致的性能下降,防止生产中断
- 提前 30 到 60 天检测到工具磨损
- 不良率最高降低 22%
- 节省 45,000 美元的人工成本
- 提前实现收入达到 900 万美元
爆胎还有积极意义?通常情况下,你会立刻收到问题预警。仪表盘上的警告灯会亮起,而你在驾驶时或者也会察觉到异样。你可以修补或者更换轮胎,然后继续驾驶,没有任何问题。这个问题仅限于轮胎本身。
然而,在许多制造过程中,情况并非如此。当模具开始磨损后,操作员往往不会意识到需要进行干预,直到出现更大的生产中断。这可能会影响生产线上的其他环节,导致产品损坏,甚至造成生产停摆。
如果操作员能够尽早识别出这类个别问题,他们就可以采取相应措施。遗憾的是,制造商往往因响应不及时而面临停机、材料浪费和产量损失的问题。
罗克韦尔自动化的团队,尤其是软件架构师 Kai Lin、印刷电路板组装 (PBCA) 工艺工程师 Miki Cvijetinovic 和 Gregory Vance,意识到这一问题给我们的客户造成了困扰,决定采取行动。他们在罗克韦尔位于俄亥俄州特温斯堡制造工厂试行了一款解决方案。
挑战
以下内容简要介绍了罗克韦尔各个基地中的电子组装作业:
- 每年出品 4,000 种独一无二的电路板设计
- 每天装配的组件达到 900 万个
- 每天产生的焊点约 2,300 万个
- 每天生产的面板数量达到 14,000 个
特温斯堡基地设有 8 条生产线,是一个大型生产基地,与其他基地一样,内部有许多可能影响生产的过程。为试行解决方案,我们选择从模板印刷过程入手。
了解过程
模板薄片上有激光蚀刻的孔径,电路板会放置在孔径下方。随后,刀片将锡膏从模板的前端推向后端,填充孔径,使锡膏能够粘附在电路板上。这一过程结束时,电路板会转移并接受检查。下一个电路板会换用另一个刀片、并以相反方向涂布。这个过程的每个环节都会生成性能数据。
超乎想象的复杂性
正如其他看似简单的制造过程一样,这其中也存在隐藏的难题。首先,模板印刷过程受多种自变量影响,导致支持人员难以检测出模板和刮墨刀是否磨损或性能下降,肉眼尤其难以察觉磨损。此外,过程启动之初以及过程中的长时间暂停会影响锡膏的有效转移,进一步增加了分析模具长期磨损状况的难度。
此外,较薄或有特殊涂层的模板,使用寿命也有所不同,磨损情况因此更加不可预测。尽管过程的每个环节都会生成性能数据,支持人员却无法实时收集和分析如此庞大的、涵盖 IT、OT 和工程多个领域的数据。
因此,支持人员需要更有效的方式来收集和分析设备的实时性能数据,并在检测到设备异常或损坏时立即收到预警。这个用例与我们的异常检测算法非常契合,印刷检查几秒后便可通过 FactoryTalk® DataMosaix™ 进行计算和显示。
解决方案
我们的项目工程师和软件团队运用算法来应对这一挑战。他们开发了一款由罗克韦尔自动化拥有的专利异常检测算法,能够实时监控模板印刷过程中的模具,并向支持人员发送性能数据。接下来,他们在该算法上实施了通知功能,使工厂人员能够即时接收异常预警,而无需进行繁琐的事后分析。
标签与传感器需求
首先,工程团队为每个模板和刀片添加了 RFID 标签,并配置了传感器来检测龙门架的移动方向。团队收集数据,并将数据与进入机器的已印刷电路板的序列号绑定,该序列号由现有可编程逻辑控制器 (PLC) 捕捉。他们还将数据与对应的模板和刀片关联,以收集关于异常、缺陷和锡膏检测的性能数据。
巧妙的数据收集和情境化
随后,我们启用 FactoryTalk DataMosaix。 这是一款精心设计的 SaaS 应用程序,能够从不同来源收集原始数据、对数据进行情景化处理再汇总到一个平台,供运营管理团队用于各类应用程序。
为何为这个项目选择 FactoryTalk DataMosaix?常规的 BI 工具并未提供足够的数据关系建模能力,也无法实时执行这类情景化处理作业。例如,Power BI 需要人工进行分析。
在特温斯堡工厂,这种分析通常是每月进行一次。有了 FactoryTalk DataMosaix 后,就可以实时执行分析,使工厂人员能够及时收到性能异常的通知。
此外,FactoryTalk DataMosaix 还会在整个生命周期内跟踪刮刀和模板在车间内的移动。通常,当模板在某一条生产线上使用时,系统会跟踪该生产线的数据; 而当模板被移出并投入另一条生产线时,过去的运行数据和性能信息往往被忽略,这样会导致工厂人员错过潜在性能问题的风险进一步增加。
借由 FactoryTalk DataMosaix,我们能够绘制数据图表,用以识别设备故障的风险。这种分析方法是一种“非常优雅的方式来观察生产线的性能”,罗克韦尔自动化软件架构师 Kai Lin 表示,“它能够明确指出生产线是变得更好还是更差。”
Teams 上的实时预警
最后,团队在 Microsoft Teams 上创建了一个频道,供工厂内部员工订阅,接收设备异常或缺陷的实时通知。预警以多种方式生成。我们选择使用 Microsoft Teams,是因为团队目前正好在使用这款业务系统。
之前的过程是这样的:当锡膏检测机检测到电路板存在问题时,操作员必须手动检查或清除问题,这往往导致判断延迟或出现错误。现在,算法能够监控模具加工设备(如刀片和模板)的性能,并针对电路板异常高的故障率触发预警,提醒操作员立即暂停并调查问题。
正是因为实施了这一解决方案,操作员才能快速确定导致故障的设备,而之前,由于生产环境的复杂性,确定问题的根源十分困难。
现在,我们来检验解决方案的有效性。工厂在 2023 年底启动了算法 FactoryTalk DataMosaix 和 Microsoft Teams 项目,收集了大概 70 天的数据。
结果
检测失败的情况减少
工程团队和工厂人员曾多次接到模板异常或缺陷的通知,并能够及时做出相应的反应。操作员不再需要等待故障发生(或在固定的日期无谓地更换模板),算法让他们能够提前 30 到 60 天收到模板故障的警告。更换或修理受损模板后,不良率减少了 22%。
操作员工作效率提高
此外,机器操作员的工作效率也得到提升。现在,支持人员能够及时收到模板问题的预警,避免这些问题影响生产线的其他部分,同时还收获了可用且有意义的数据。操作员受到的干扰减少,工作效率随之提升。
特温斯堡等地的高投资回报率
在特温斯堡基地进行 4 个月的评估之后,我们计算出每年节省的人力成本远高于项目成本,投资回报率约为 200%。随着更多使用案例的规划,我们有理由相信 FactoryTalk DataMosaix 的投资回报率将继续提升,使年度支出物有所值。
收入显著增加
最终,不良率的降低以及工作效率的大幅提升带来了收入的增加。确切地说,此举使工厂的中断减少,因而得以尽早实现价值 900 万美元的收入。
前景光明,成果丰硕
算法与 FactoryTalk DataMosaix 整合的未来会如何?工程团队和软件团队正在密切合作,推进特温斯堡的规模化部署,并将该做法推广到梅克旺、蒙特雷和新加坡的工厂。我们也期待在自己的工厂应用这一解决方案。
由于罗克韦尔自动化拥有这一算法,我们可以为客户提供的应用场景几乎是无限的。正如 Kai Lin 所说,“当你考虑算法能提供什么时……然后真正将算法与过程中的工具性能监控关联起来,我认为它在离散制造领域将大有可为。”
发布时间 2024年6月26日